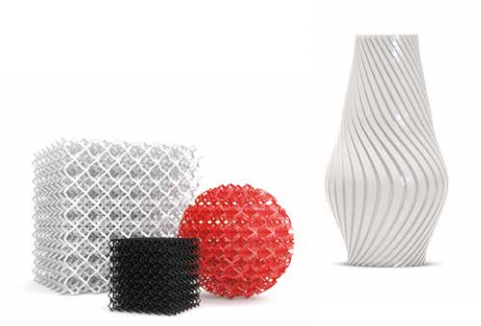
In fairy tales, a wizard waves a magic wand and poof! There’s a carriage or a cake or a pair of shoes. We don’t have magic wands, and probably never will. But we do have 3D printers. A 3D printer can’t make something out of nothing. But it can create just about anything you can imagine. Feed one a design for an object, and it will print that object. You just have to give it a raw material to print with. Many 3D printers are small machines—around the size of a microwave oven—so they can be carried anywhere.
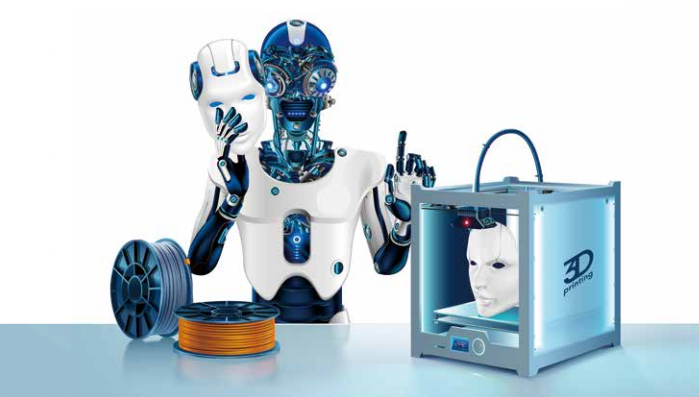
Someday, when deciding what to wear in the morning, you might be able to walk over to a 3D printer, customize an outfit, and then print out something tailored exactly to your size, mood, and personality.
All Shapes and Sizes and Styles
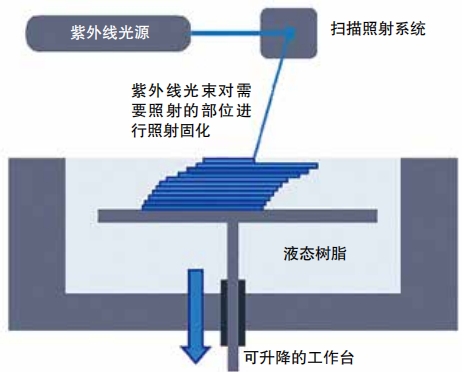
3D printing is the common name for any process that builds an object by adding material bit by bit, following a computer design file. The technical name for this process is additive manufacturing. 3D printers come in all shapes and size—smaller ones print toys, precise parts (including circuit boards for electronics), or even patches of human skin. Very large ones print buildings or other architectural features.
3D printers can build objects from a dizzying array of materials. Polymers (e.g. plastics) are the most common printing materials, b ut printers can also create objects from metal, ceramics, dough, concrete, and more. Bioprinters print with living cells or biological materials to create skin, bone and more.
3D printers use several different methods to build objects. If you have ever used a 3D printer at school or elsewhere, it was most likely a fused deposition modelling (FDM) printer. An FDM 3D printer squirts a soft material (typically hot, melted plastic) onto a surface, building an object layer by layer. As the plastic cools, the object hardens. Food printers follow a very similar process to create 3D-printed cookies, candies, and more. Architectural printers squeeze out concrete-like materials that harden to create structures. Many bioprinters squeeze a special gel containing living cells from a syringe to build biological structures. These are all FDM printers.
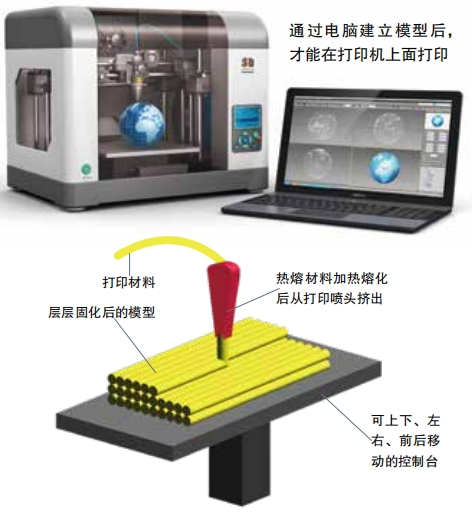
Stereo lithography (SLA) is a 3D-printing method that uses light. The raw material is a liquid, typically a plastic resin, that stays liquid until a certain type of light hits it. In an SLA printer, a moving laser beam draws a shape on the resin, hardening only the parts that the beam touches. Next, a platform lowers this first layer of hardened resin, and the beam draws the next layer. As the platform moves down, the beam keeps hardening the resin, layer by layer.
Selective Laser Sintering (SLS) or Selection Laser Melting (SLM) is similar to SLA. Instead of liquid resin, powdered plastic, metal, ceramic, or glass is used. A laser heats the powder layer by layer, fusing it into a solid object. The final part ends up buried in unused powder. “When you’re done with these machines, you’re digging through them like a treasure hunt, picking out your parts,” says Greg Paulsen, an engineer at Xometry, a company that makes 3D-printed parts for manufacturers.
Digital Light Processing (DLP) printers use a liquid resin but no lasers. Instead, a screen like the screen on a tablet sits between the resin and a light source. The screen blocks all the light except for the shape that needs to be drawn. DLP can create very fine details, and it prints very quickly because it draws each layer all at once. Jonathan Allers, host of the YouTube channel Destructive Creativity, used one of these to print a small cathedral. It came out much nicer than one he had printed on an FDM printer, which can’t print details smaller than the width of its nozzle. “Look at the detail on this thing!” he remarked. “You can actually see the details inside the stained- glass windows! This is phenomenal. ”
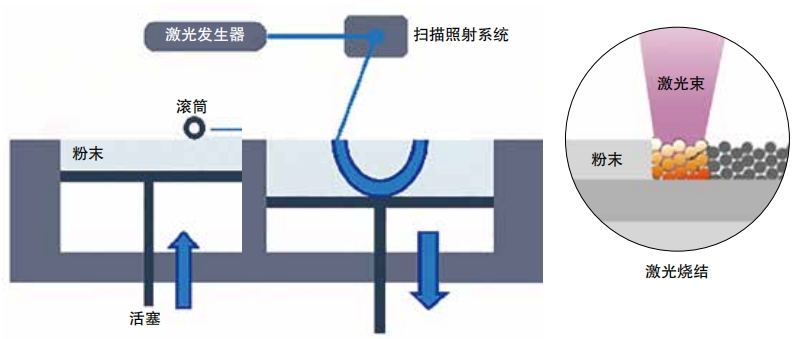
Each of these 3D-printing methods has many variants, and new methods as well as new raw materials are being developed all the time. Most 3D printers today print in just one material. But printers that can combine multiple materials are also being developed. One that already exists can build with fourteen different types of plastic. Though all of these materials are plastic, they have different colors, strengths, temperature ranges, compatibility with the human body, and more. To build an electronic device on one machine, a 3D printer will have to combine different types of metal, ceramics, plastic, and other materials.
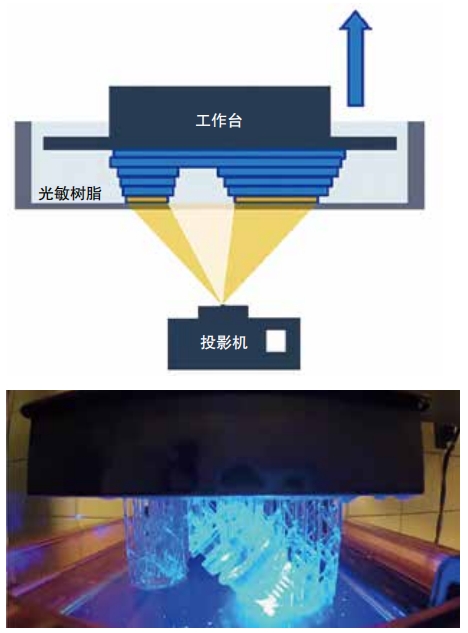
Multi-material printers will also allow the development of brand – new materials that aren’t possible to produce any other way . In their book, Fabricated: The New World of 3D Printing, Hod Lipson and Melba Kurman write, “The versatility of what you can make on a 3D printer will grow exponentially with the number of primary materials that can be printed and mixed simultaneously. ”
Before and After Printing
Even the fanciest of 3D printers can’t do a good job unless it has good instructions. Those instructions come from a design file. A 3D printer without a design file is like a piano without anyone to play it. Just as the skill of the piano player makes a huge difference in the music that comes out of a piano, the skill of a designer makes all the difference in the finished product made on a 3D printer. “Design software is the heartbeat of 3D printing,” write Lipson and Kurman.
Most design software that exists today was created for traditional, subtractive manufacturing. In this type of manufacturing, machines cut away material to form parts, or pour material into molds to harden. Machines follow instructions from a CAD (computer- aided design) file. Traditional CAD software does not describe the interior of an object because the inside is usually solid material. 3D-printers, however, can print structures on the inside and outside of an object. This means they can create stunningly complex interlocking patterns and lattices. Design software to create this type of structure does exist, but it isn’t always easy to find or learn.
Most 3D printers today require a file type called an STL file. It describes the geometry of the surface of the object using a mesh of triangles. The smaller the triangles, the higher the resolution. Animators who make 3D video games or movies use this same type of modelling to create 3D virtual characters.
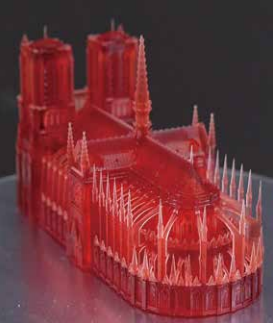
The objects that come out of 3D printers aren’t completely finished. They all require some amount of clean- up and polishing, which is called post- processing. One issue is that most 3D-printed objects require support structures. For example, if you are printing a tree, branches that extend outward from the trunk will need printed pillars to hold them up as they cool or else the tree would collapse. These support structures must be cut away. Most 3D-printed objects have a rough or textured surface. Some contain lines left behind by the layered process of printing. These textures are usually polished or sanded away.
A Whole New World
In traditional manufacturing, precisely engineered machines churn out many copies of a single part. These parts then travel to factory assembly lines where more machines and workers connect the parts to form finished products. Most factories are located far away from the people who need the parts or products, so ships, planes, and trucks carry all the stuff around the world. Factories and assembly lines produce many identical parts and finished products very cheaply. Making complex items, unique items, or a large variety of items is expensive. Oversupplies and shortages can happen when a factory makes or ships too many or too few items.
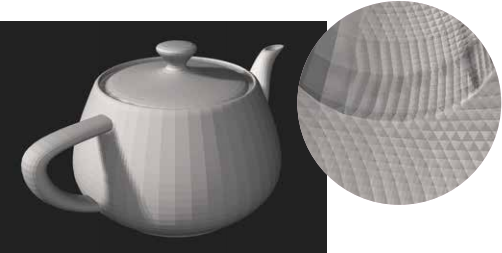
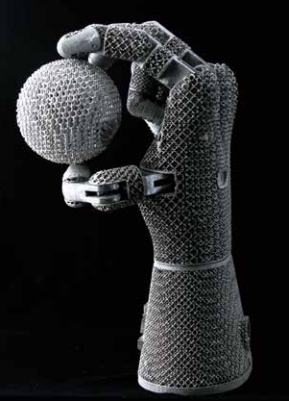
3D printing has the potential to improve on this situation; however, it is a fairly new technology so it has some problems. 3D printing is often painfully slow. “There are mushrooms that grow faster than 3D-printed parts,” said Joseph DeSimone, CEO of Carbon3D, in a 2015 TED Talk . Also, the process of laying down material layer by layer often creates weak objects. The materials available for 3D printing have been limited. And 3D printing most products is still way more expensive than using regular factories and assembly lines. Still, many engineers, inventors, d es ig n e r s , a n d oth e rs u s e 3 D printers to print prototypes (or samples) of products with new designs.
3D printers are improving by leaps and bounds in speed, ability, versatility, and cost reduction. DeSimone’s talk introduced a printer that uses a digital light processing technique to make objects up to one hundred times faster than earlier machines. These objects are also much stronger than traditionally-printed objects because the object hardens all at the same time. “If you actually make a part that has the properties to be a final part and you do it in game-changing speeds, you can actually transform manufacturing,” said DeSimone. In the future, 3D printers may largely replace traditional factories, assembly lines, and supply chains. People will engineer, build, transport, and shop in totally new ways . Objects themselves will come in shapes and have properties that weren’t possible with old manufacturing methods . In Hod Lipson and Melba Kurman’s book, Fabricated: The New World of 3D Printing, they outline some of the aspects of 3D printing that could change the world. Here are some of the ideas they mention.
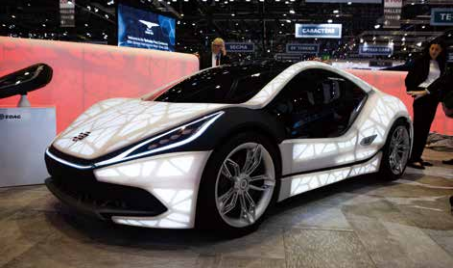
1.Complexity and variety are free.
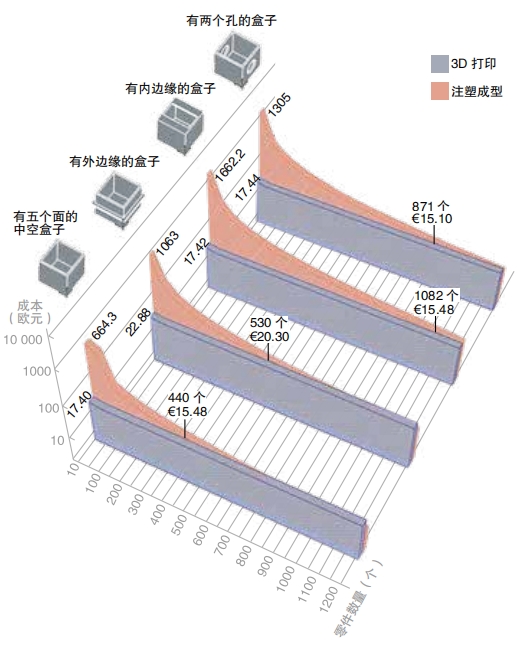
只有当批量到达某一个值时,平均成本才低于 3D 打印
On a 3D printer, producing a set of identical plain, boring cubes takes the same amount of time and energy, and costs the same, as producing an assortment of intricate snowflakes, each unique. In traditional manufacturing, each snowflake would require a different mold, or unique adjustments and perhaps even unique parts for the machines used to make it. The 3D printer does need a new design file for each new object, but design files are virtual and therefore practically free to modify, store, send, and copy. No machine shop required.
People are used to paying more for complexity and customization . In the future, the cost of an object will no longer need to be linked to its intricacy or uniqueness. The amount of material or the cost of materials will likely matter more . Also, people will have more access to goods made just for them, to their unique sizes, styles, and tastes.
2.No assembly required.
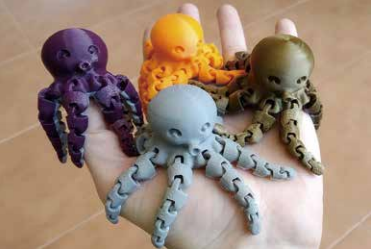
A 3D printer can join parts together as it prints. On an assembly line, parts must be glued, fastened, snapped, or welded. Think of a box with a lid that opens and shuts. The hinges for the lid are made separately and then attached to the box and lid. A 3D printer could make hinges that are already attached, greatly simplifying the process of producing the box. Javi Rodríguez, a maker who goes by the name McGybeer on the website Thingiverse, designed a cute toy octopus with flexible tentacles . The tentacles contain joints that connect together as the piece prints. There are no seams and no hardware holding the joints in place. Moving parts that are printed already joined won’t break apart as easily.
New 3D printers will even be able to combine different materials in one print. That means manufacturers won’t have to assemble many parts into a finished product. Multi-material printing will make new objects that can’t currently be created possible.
3.On-demand, portable, unskilled manufacturing.
A 3D printer can make items only when and where the items are needed. The current supply chain often leaves people with stockpiles of items they can’t use or long waits for items they need but can’t get. Time and resources are wasted when items aren’t in the right place at the right time. A 2018 study estimated that in the UK alone, 100 million hours are wasted each year dealing with supply chain inefficiencies. Hauling items in trucks, planes, trains, and ships also costs an astronomical amount of money and worsens climate change. What if the world didn’t need to send so many goods all around the globe?
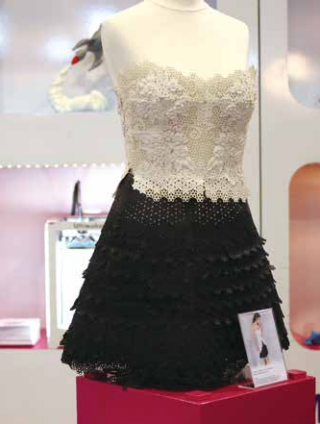
Each town—or perhaps even each home—could have a dedicated 3D manufacturing site to make everything everyone needs . It wouldn’t even need to look like a factory. It could look like a boutiqueshop, with screens where people order clothes or shoes that fit them perfectly or appliances that fit perfectly in their homes. The only things that would need to be delivered would be raw materials for the 3D printers. The printers could even produce the parts needed to maintain and repair themselves.
As long as people had access to good design files, they wouldn’t need any skills to use these machines. Eventually, a small 3D printer could be carried around or used in a home or office to make everything people need only when they need it. Some types of 3D printers can even make objects bigger than themselves, such as buildings. Skilled builders may no longer be needed for construction projects.
This isn ‘t go i ng to happe n in the very near future . At first, manufacturers will use 3D printers to shorten their own supply chains, meaning they won’t have to wait as long for parts or repairs . “You’re not going to be sitting in your home, printing out exactly what you want to repair your car any time soon, but major manufacturing companies are really adopting this technology,” Jennifer Lewis, a materials scientist at Harvard University in Cambridge, Massachusetts, told Nature.
4.Object copying.
3D scanners already collect information about real world objects in order to create highly realistic virtual objects. These virtual objects are very useful in virtual reality. When paired with a 3D printer, though, virtual objects can become physical ones . Imagine a museum director scanning in a Tyrannosaurus rex skull and someone printing out an exact copy to decorate their home. The digital revolution has already changed how people access music, books, and movies . We now have access to a practically unlimited supply of all media. The same sort of thing may soon happen for physical objects.
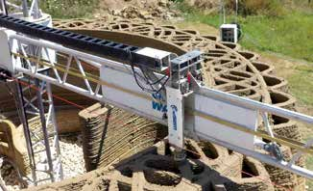
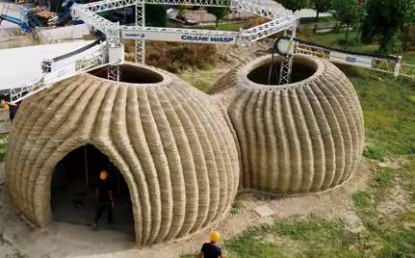
5.Reduced waste.
When factories produce too much of an item, the extras may go to waste. In addition, subtractive manufacturing, especially of metal, leaves a huge amount of valuable material on the factory floor as waste. Plus, the current supply chain is hugely wasteful in terms of energy, time, and effort. 3D printers have the potential to greatly simplify the world of manufacturing and reduce its waste.
Problems to Consider
3D printers aren’t perfect. They tend to require a lot of electricity to run. They also generate waste, include support structures that must be removed. And the most common raw materials that feed them are plastics that pollute the environment.
If people could make whatever they wanted easily and cheaply at any time, might they use that power to churn out piles of stuff that they don’t really need? Might they stop carrying or re-using items and print out new items instead? Imagine going on a trip and bringing along no luggage because you could just print everything at your destination. This could cause a serious trash problem, even worse than the one we’re facing now . Ideally, 3D printers of the future will be able to work with recycled plastic or even take in printed items that are no longer needed in order to transform them into new items.
With 3D printers, it will also be very easy to copy products without permission. Consumer protection and regulation of product safety may become much more difficult. People may end up printing faulty items and getting hurt. And some are already experimenting with printing weapons, drugs, and other harmful items. Like any technology, a 3D printer is a tool that can be used for harm or for good. Laws and restrictions will have to be put into place to help limit harmful uses of the technology.
Still, the possibilities of this technology boggle the mind. A 3D printer could construct a home in one day, putting in all the pipes and electrical wires at the same time as the walls and support structures. Imagine how much this could help people who have lost homes in a disaster. A 3D printer could allow for the immediate repair of any machine as long as a person (or robot) who knows how to perform the repair is available. Someday, 3D printers could even help craft entire meals filled with foods that weren’t possible to create with traditional cooking methods . It will be eye-opening to see where this technology takes us.